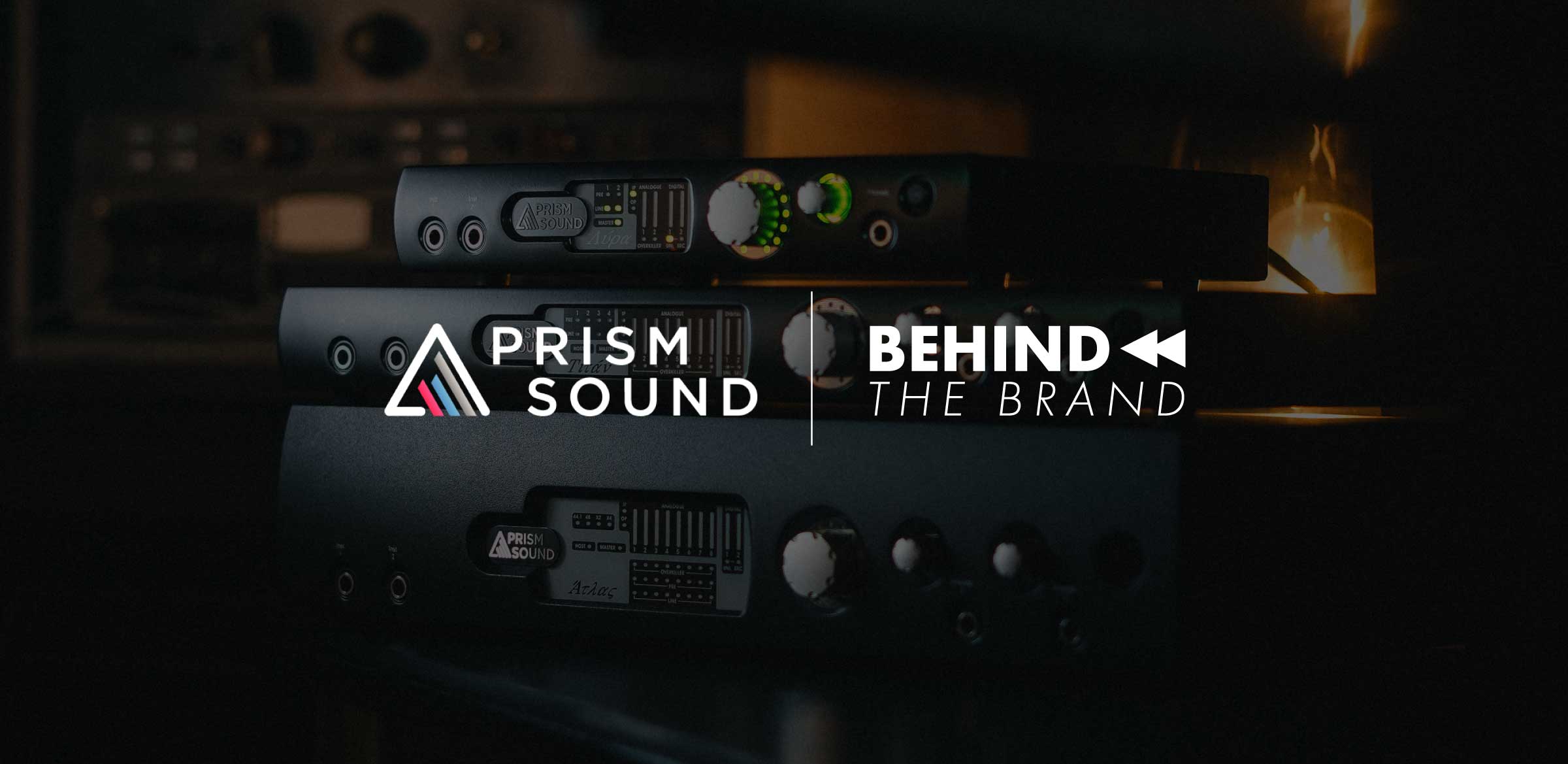
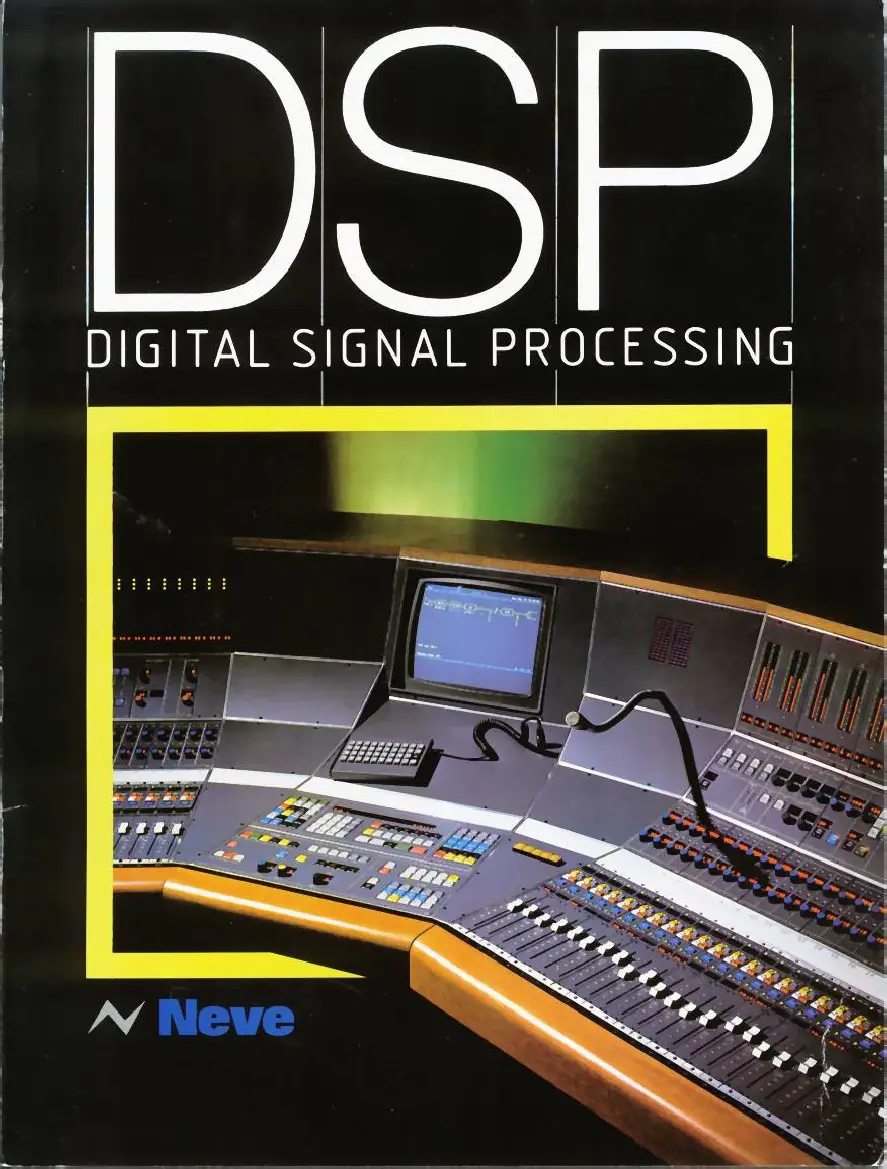
Prism Sound | A Brief History
The phrase “no-compromise” is one that gets bandied about frequently nowadays, but for Prism Sound it has always been a mantra that rests firmly at the core of their design philosophy. For over 30 years they have been manufacturing and supplying some of the world’s finest converters to top engineers and studios across the globe, establishing a reputation as the reference point for accuracy, unparalleled performance and product longevity. Indeed, every Prism product is seemingly built with “future-proof-ability” – not profitability in mind.
The origins of the company can be traced back to 1981, when two electronics engineers, Graham Boswell and Ian Dennis, crossed paths. Boswell and Dennis cut their proverbial teeth working on digital audio technology and product development at Neve. At the time there were no dedicated audio DSP chips available on the market, and so with the help of government funding Boswell and Dennis set about developing a solution. It was from this that the world’s first commercially available DSP console was born; the Neve DSP.
Around 1987 Dennis and Boswell eventually left Neve, set up Prism and went on to provide professional digital audio consultancy, offering their expertise to a varied range of fields. From military spec radar systems (featuring high precision A/D conversion for azimuth measurement in the antenna) to the world’s first all-digital commentary and communications switching matrix commissioned by the BBC for the ’92 Barcelona Olympics, they were involved in a number of unique and innovative developments.
The Early Days
Whilst these projects spanned a range of industries, 1993 to 2000 saw a general shift in Prism’s direction, however, when they began to focus on studio-grade products aimed specifically at recording facilities. CD releases were booming, triggering a demand within the recording community for higher resolution conversion that could take full advantage of the medium. Converters such as the AD-1 provided a huge step up in dynamic range and low-level clarity compared to what was typically available on the market at that time. The AD-1 laid the foundations for future products to build upon, such as the AD-2 and DA-2 which soon followed and introduced the capability to record at previously unheard of sample rates of up to 96kHz. The AD-2 was a remarkable achievement, quickly becoming the converter of choice for seasoned mixing and mastering engineers the world over. So high was the quality that these converters offered that some even ended up in the secretive world of intelligence gathering, where the best possible noise levels and greatest clarity were required!
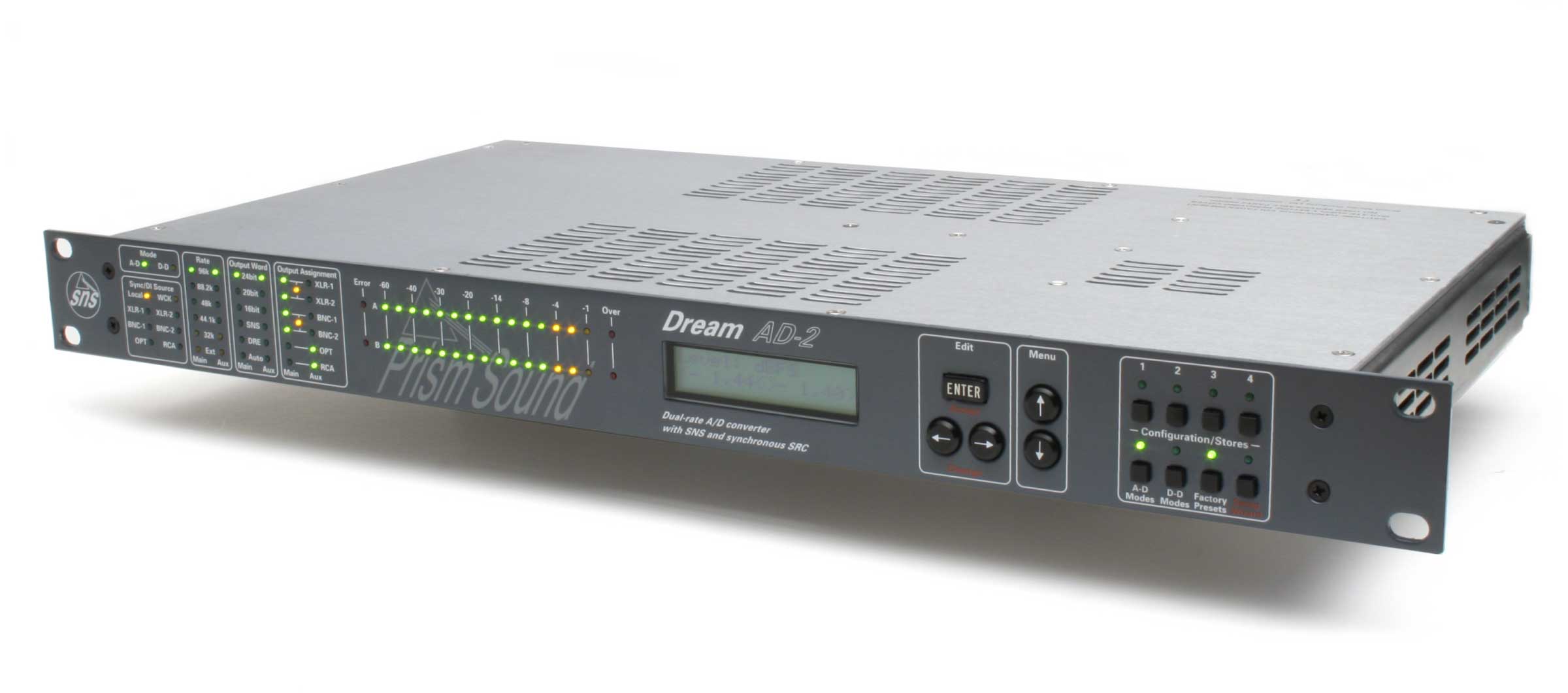
Building a Legend | The Dream ADA-8 & ADA-8XR
As studios required higher channel counts and greater flexibility to accommodate larger multitrack sessions, it wasn’t long before Prism Sound answered the call, and so the ADA-8 AD/DA converter was born. This modular unit could accommodate eight channels of conversion in each direction or up to 16 channels of eight A/D or D/A. It marked a big shift in focus to the wider recording market, and has gone on to become one of the most successful and long-running converters ever made. The ADA-8 was eventually updated to the ubiquitous 8-“XR” which offered new sampling rate capabilities up to 192kHz. To this date, the ADA-8XR can be found in leading studio facilities the world over and is widely regarded as being on of the finest converter systems ever made.
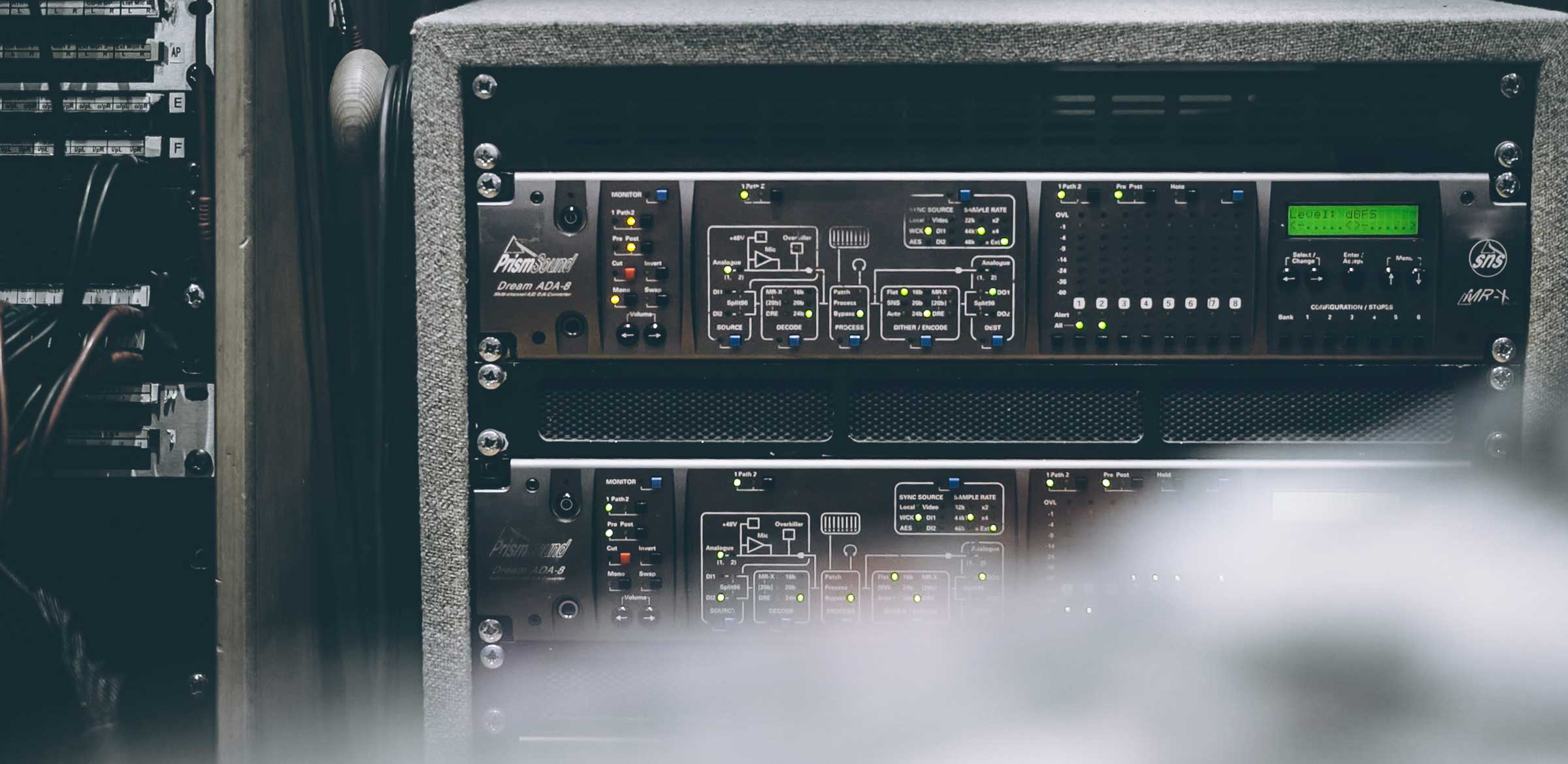
The Rise of Orpheus
Prism’s shift in focus was also underlined with the introduction of Orpheus; a radical departure from the somewhat functional and utilitarian-looking boxes often associated with “converters”. The Orpheus was aimed at the home studio and desktop audio market, delivering the same chip technology that ensure superior transparency and accuracy, and marrying it with high quality preamps, Firewire connectivity, a user-friendly and interface and other typical interface features such as headphone amplifiers and ADAT connectivity. It was an instant hit, and would later evolve and split into three separate models: the Lyra, Titan (effectively an Orpheus with USB) and Atlas Interfaces.
Uniquely, it can be argued that every product that Prim have ever released was the direct result of listening to the market and more specifically, to the demands of their customers. This approach to innovation is no better illustrated than with the announcement of their latest offering, the Dream ADA-128. The idea for the ADA-128 was cultivated from conversations with The Royal Birmingham Conservatoire. These discussions led to the development of undoubtedly Prism’s most ambitious and fully-featured converter system yet. With a modular design, multiple clock source capabilities (enabling large facilities to operate multiple separate recording setups at once), and the ability to handle sample rates of up to a whopping 798kHz, it offers a remarkably future-proofed solution for the most discerning and demanding applications.

Whilst Prism now operate as part of the Audio Squadron family, they continue to operate, design and manufacturer their products here, in the U.K. We sat down with Sales Director Mark Evans to discuss what makes Prism Sound different, and how the new flagship Dream AD-128 embodies the same founding principles on which the company was built…
Much has changed in the world of technology over the past few decades, and I guess the early years looked very different to Prism Sound as we now know it. How did it all start?
Graham and Ian were contract engineers woking for Neve, originally. They developed the first DSP-enabled console with the Neve DSP console, and then as part of another contract job they had to design a converter. This was 35 or so years ago, and they designed a converter that performed so well that essentially there was nothing on the market that can measure it. And so they went off and designed a piece of measurement equipment. It was from those sort of humble beginnings that the two parts of the company formed. One was test and measurement, and the other was recording and production.
I suppose from a manufacturing point of view, those two things go hand-in-hand, right?
Yeah, It makes us very unique as a company. The reason I say that is because an awful lot of our competitors use our products to design and build their products. And that includes other converter companies. They use Prism test measurement products to help design and test their own products. So because of that we have to understand the technology differently to everyone else. If you’ve got a product that measures from 0 to 100, and that’s as good as it can ever be, then of course the test measurement equipment has to be able to go to from 0 to 110. It’s that experience that it allows us to understand the products that we make on a deeper level to most.
That must give you an interesting point of perspective regarding competitor’s products and the market in general…
Well, what it does help us to understand is that not all the glitters is gold. By that I mean there are ways of measuring things to give you really good numbers on paper, right? Whereas the reality is often something different. All of us converter companies have the same components available to us, yet somehow we are able to create a product that offers better performance and is more accurate. And you sort of have to ask, why is that? The analogy I often use is a Michelin Star chef. Put us in the same kitchen with the same ingredients and what they’re going to produce is gonna be a lot tastier than what I’m going to cook you. I mean, the thing that we do differently to most is we pay absolutely meticulous attention to every part of the product and the relationship between the individual components – not just the components themselves.
It’s about the sum of the parts and not just which converter chip you’re using.
Right. People often get very hung up on which chip is used. Of course you have to choose a good one, but you’ve still got to know what to do with it. Everything from the way the power flows through the unit to the way that the tracks are laid out in the circuit board and the way that the clocks run etc… you have to get all of these things right. Only then do you end up with a product that performs as efficiently and sounds as good as a Prism. One of the things I often think makes us a bit different from everyone else is the way we set about designing our products. A lot of other manufacturers start off by saying; “right, we want to make a product that has 10 in, 10 out, with an AES connection, and we want to be able to sell that for £1000”. And that’s great, but by doing it this way and setting the retail price at the start, most of the design and component choices have already been made for you, because in order to hit that price point, you’re forced into designing the product to meet a specific manufacturing cost. Whereas the way Prism design products is we start off by deciding on the I/O just like everyone else, but then we just design the product to perform as well as we can possibly make it. Once we know how much it’ll cost to build, we set the retail from there.
…and then they cost what they cost. Most seasoned engineers will know about Prism in one way or another, but do you think there’s a challenge in encouraging a new generation of engineers and producers that that difference in quality is worth the investment?
It is a challenge. When Orpheus came onto the scene, the mass market became much more aware of who Prism sound were as a company, and it really moved the company in a different direction. Everything prior had been very high performance products. They were fearsomely expensive. And this was suddenly a product that had performance that blew everything out the water. It performed as well, if not better than an AD/DA-2 and ADA-8 but could be bought relatively inexpensively. I think as, as much as anything, it was the right product at the right time, and a much wider demographic of people were, and still are, realizing that a high-quality, high-performance converter makes their work more efficient, and in many cases, easier. Critical mix decisions can be made with confidence – what you are hearing is faithful to the source, which is key.
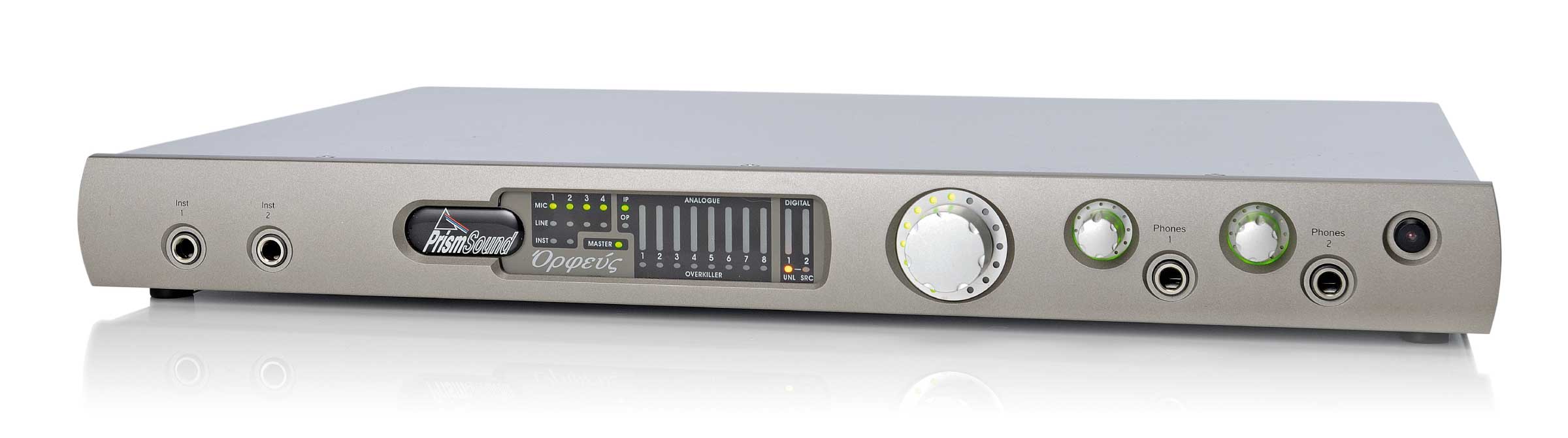
I always took for granted the difference a high quality converter could make until I was able to compare them directly at Funky Junk. Everything from the stereo imaging to the dimension and depth of sources changes. I think people are starting to understand that it makes a perceivable difference.
There’s a lot of marketing out there that says, this product’s good, this product’s accurate, this product’s transparent. And actually, in a lot of instances, it sort of really isn’t. One of the sort of slightly strange problems that we run into continually is people will put in a Prism sound product having thought that a product they previous used was very accurate and “flat”. Then they put in a Prism and actually the feedback they come back to us with is well, you know what? It’s lacking in bass or high-end or the mid-range sounds weird because what they’re hearing is an accurate – but different – representation of the sound. It can sometimes be an eye-opener and in some cases, a tough pill to swallow.
How do you respond to that feedback?
We get people to do the “Loop-through” test, which just basically means you go out the converter, back in and back out again. You flip between those two paths and if you can hear a difference, the converter is doing something to the sound. We get people to do that with with any converter. With Prism products, you can’t hear a difference. With a lot of other products, you can. So a lot of what we try and do is actually education. It’s about helping people understand why this stuff matters.
The ADA-8XR was, and still is, an incredible product that has remained a leading converter for decades – an achievement no other converter can claim. Why do you think that is?
The testament to ADA-8 goes back to this meticulous attention to detail. Even if you get an incremental gain five years down the road from a new chip, if you haven’t got all of these other things absolutely perfect, you’re not necessarily gonna get an improvement in quality. I mean, we go to great lengths to design products that are going to last. We want people to still be using our products in 10 or 15 years. Buy it once, buy it right. And if you do the maths, then actually Prism sound products really aren’t that expensive. Compared to a products that requires you to upgrade two years down the line, and then two years after that, and then two years after that, the Prism will still be leading the performance charge after all those years. It offers a huge return on investment, and we have this in mind when we design things. Take the new Dream-128. I mean, the chassis itself operates at sample rates up to 768kHz. No one’s doing that. There are no chips on the market that can go that high, right? But it’s important to us that when they do arrive, you don’t have to go out and buy another box. You can just put some new firmware on it and stick a new DA card in and it will just work. So that future-proofing is a huge consideration when we are designing products.
Could you touch on how the idea for the 128 came about, and and what some of the initial conversations looked like?
It actually grew from conversations between Managing Director Jody Thorne and the Birmingham Conservatoire who needed large amounts of really high-quality I/O for their enormous state-of-the-art facility. They needed a lot of – I don’t even know if this is a word – “share-ability”. Colleges, maybe more than your average recording studio, change things almost on a daily basis, depending on the classes that they’re teaching and things like that. So they needed a product that could adapt and change to differing recording situations without having to completely rewire the whole thing. You needed to be able to change configurations and how the I.O was set up seamlessly, and all of this over a large number of channels.
ADA-8XR would’ve been an option, but when, when you start adding up the sort of cost and vast amounts of AD/DA needed, both in terms of cost and physical space, it became sort of clear that this wasn’t going to be an option. And so we had those conversations, came back and then the genius that is Ian Dennis went away and came up with this fully modular, massively future-proofed high-quality, high-density product. But because Ian is so smart, he then sort of surprises us with little additions, like, “you know what, I can give this four clock circuits, right”?
Was that a totally unique concept at the time? I’m not familiar of anything else that’s able to sort of do that in a single unit.
Yeah, it opens up a whole new realm of possibilities and applications. A studio who has a single machine room and multiple studios can say, right, today we need 24 in / 24 out in Studio one, but we only need 8 in 8 out in Studio two. Well, now you don’t need two different boxes to do that.
Something that is often overlooked though, and the really smart thing about 128, is that, broadly speaking, you can make something very, very good quality if you give it an absolute ton of power. Right? The thing about 128 is you’ve still only got a finite amount of power going in, but the way that power is distribute results in no compromise in quality, despite the huge amount of channels. That’s really the most clever thing about the box. You’ve got to account for every last thousandth of a watt, knowing where every single bit of power is at any given time. There’s nothing inside that unit that doesn’t have a specific purpose or reason for being. Every single component and everything chosen has its function.
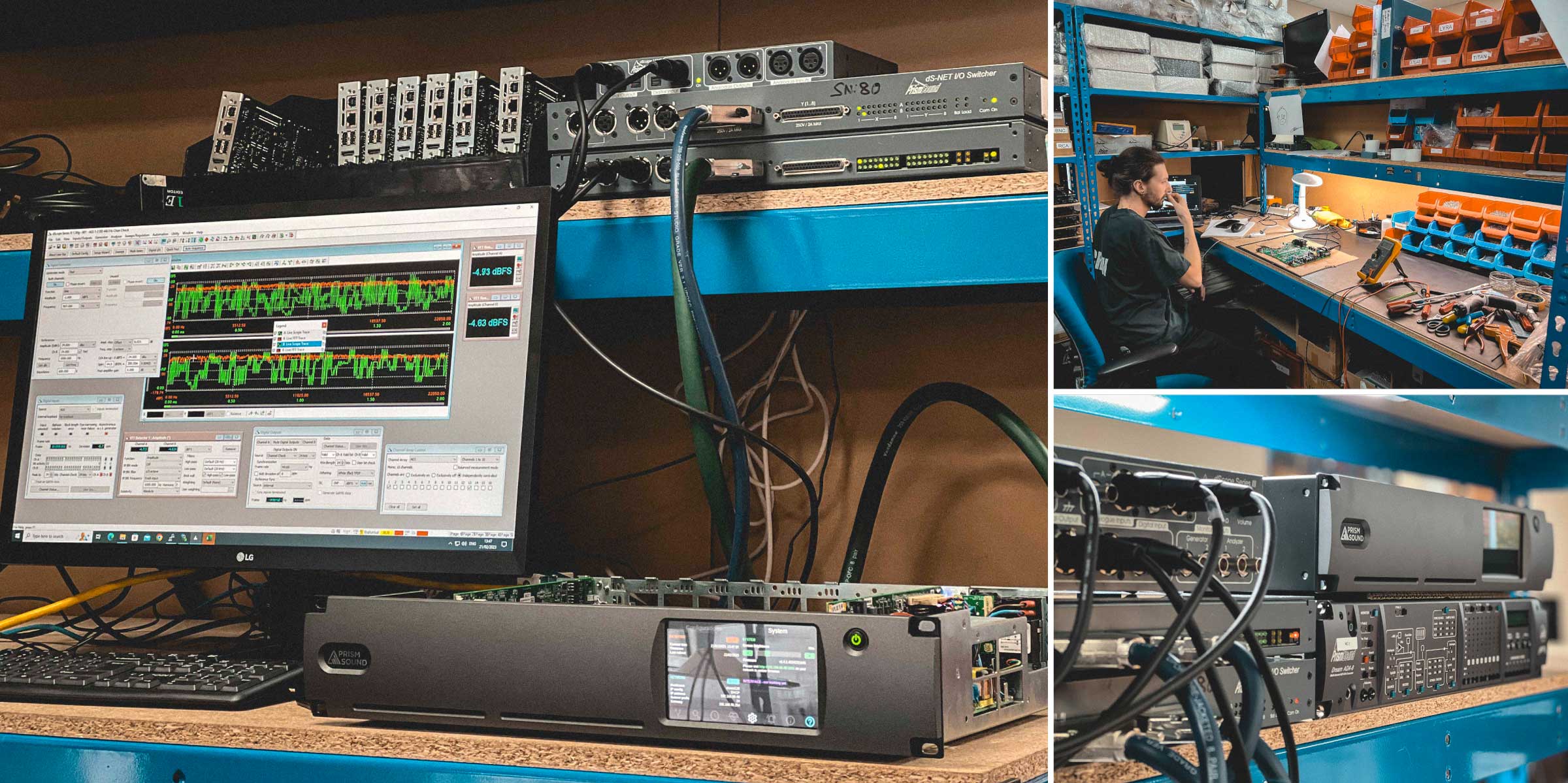
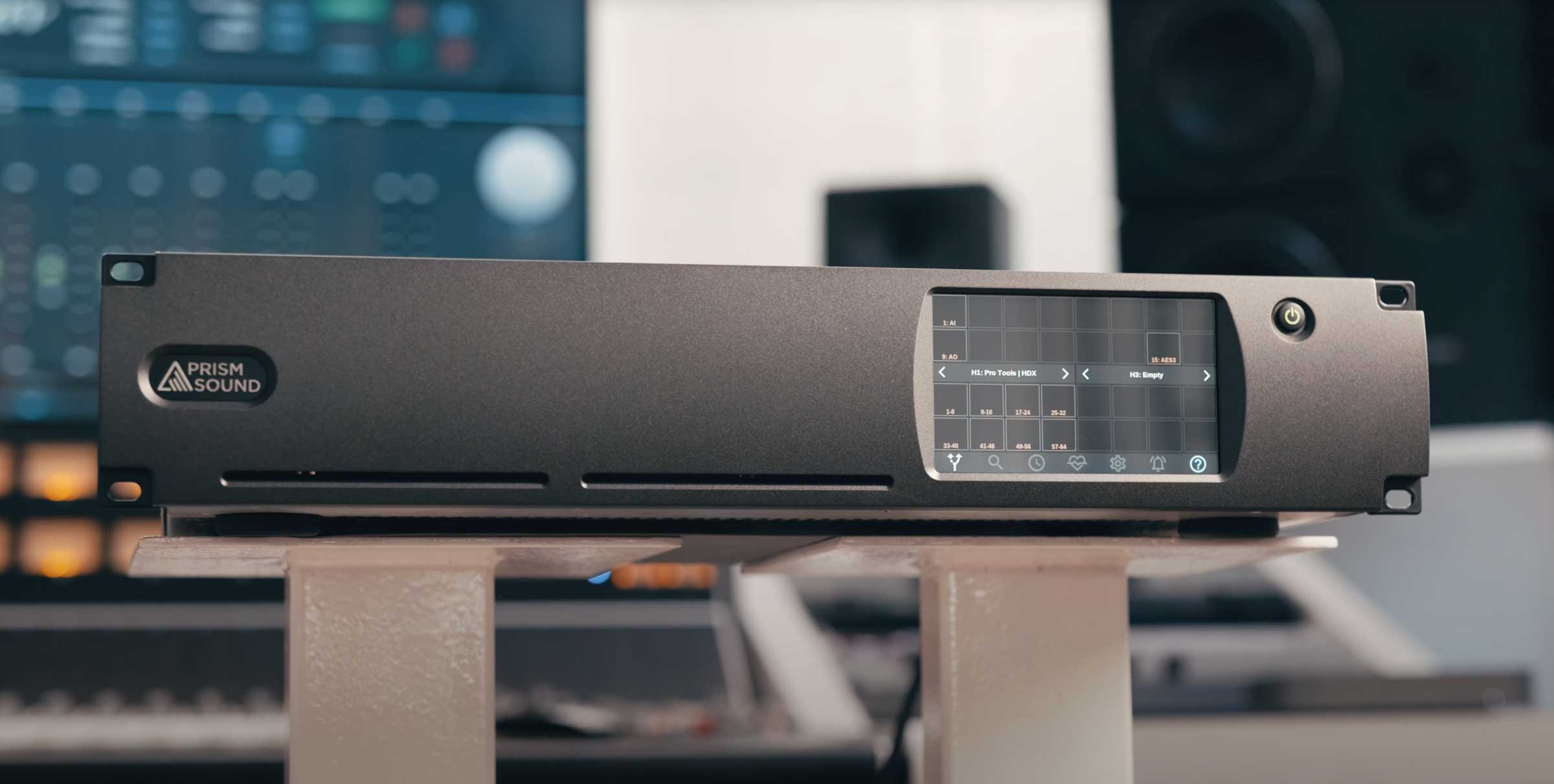
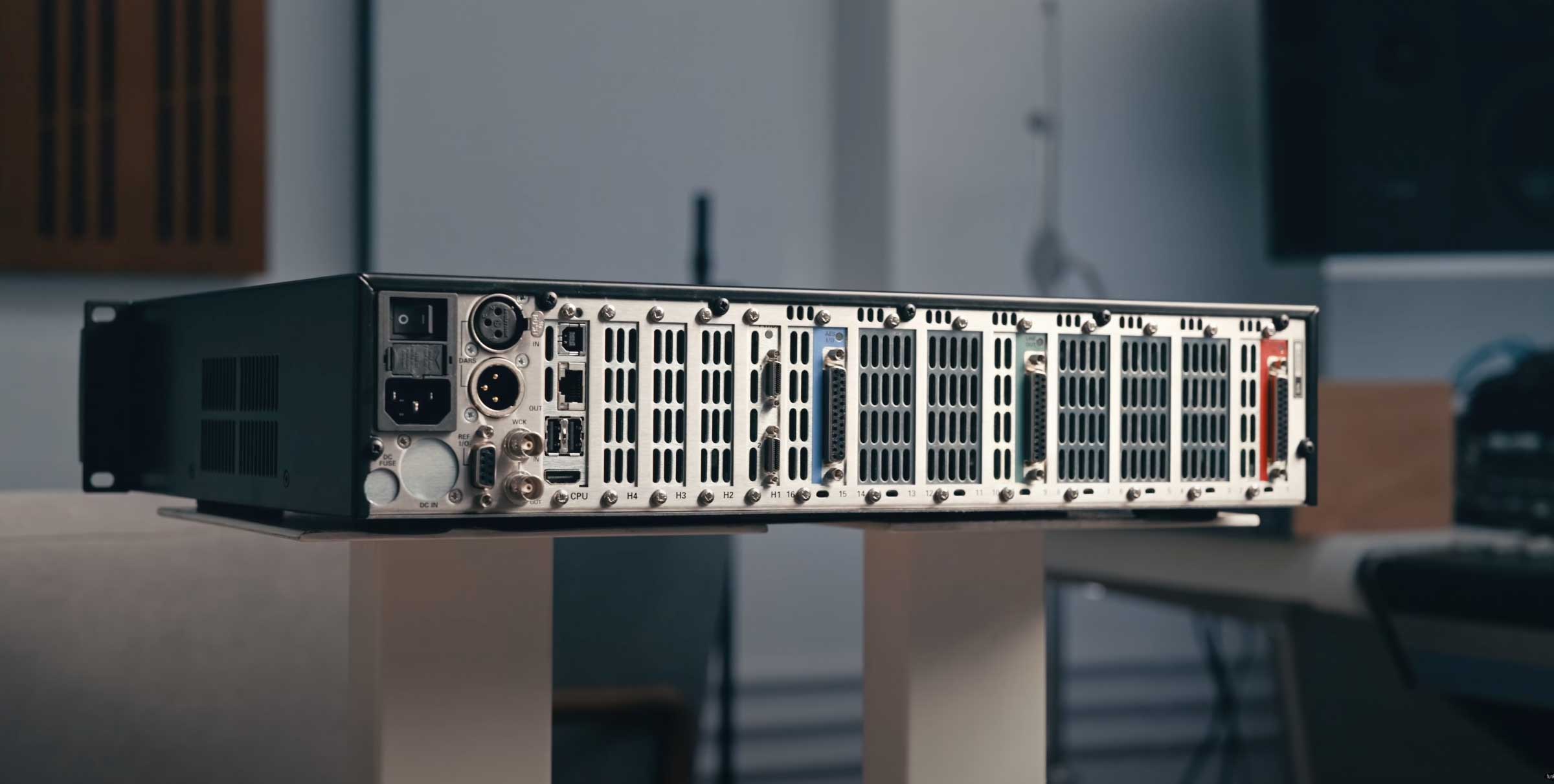
Would it would be fair to say there were some challenges along the way?
Honestly, we would struggle to think of a more challenging period for development. And I mean, this wasn’t just us. Everyone during that time suffered these problems. Again, part of the reason the product was so delayed was of course due to the pandemic and the subsequent knock-on effect that had, but also because of our attitude and reluctance to cut corners. I mean, it would have been easy to just use a replacement component that made a 0.0001% difference, but that’s just something we weren’t prepared to do. So, if we couldn’t get a component or we had to change something, it had to be equal to or better than what we’d taken out. And throughout the period of development, there were tons of things that we had to do that with. And so in a weird sort of way, we actually ended up with a product that was better than we’d ever set out to make.
So you were indirectly learning more about your product as you had to adapt to the situation?
Right. And we had all of the same problems others were facing too. I mean, little things like cardboard being in really short supply for boxes because, out of every thousand boxes that went out, 999 of them went to Amazon. Metal work was difficult to get, paint was hard to source. I mean, you really couldn’t have picked a more difficult period to design and manufacture a new product.
But thankfully, here we are! And it’s shipping… Have you started getting some feedback from early adopters?
Absolutely! It’s been very positive. Generally speaking, we leave the listening of our products to people with ears that are far greater than ours. We make a product that is the best that we can possibly make it, and we leave it to other people to compare it. So we never compare, we don’t plug in a 128 and compare it with a Lyra or compare it with an AD-II ourselves. Of course, when you get to these top levels of performance, the differences are small. Many of our top clients who had our previous ADA-8XRs use a 128 and say, you know what? It is better, but it’s not like going from being in a dark room to switching the light on. I think if there had been a vast sonic difference between that product and our previous products, people would’ve been concerned.
But the Dream-128 offers so much more than just better conversion technology, right?
Yeah, precisely. Consider our larger Prism customers, people who have 20, 30, 35 ADA-8s. If you’re gonna replace eight ADA-8s, that’s 16u of rack space plus a space above and a space below each one. So you’re getting on to 25u of space. Whereas a 128 occupies 2u with a space above and below. Then consider the cost of running eight ADA-8s (which can run hot!) compared to a single 128. The financial savings in cooling alone are huge. Add to that the fact a single 128 can accommodate the full HDX channel count of 64×64 means you don’t need to buy 16 Digi-Link cables to connect your eight ADA-8s! It all adds-up to being a very cost-efficient and economical package.
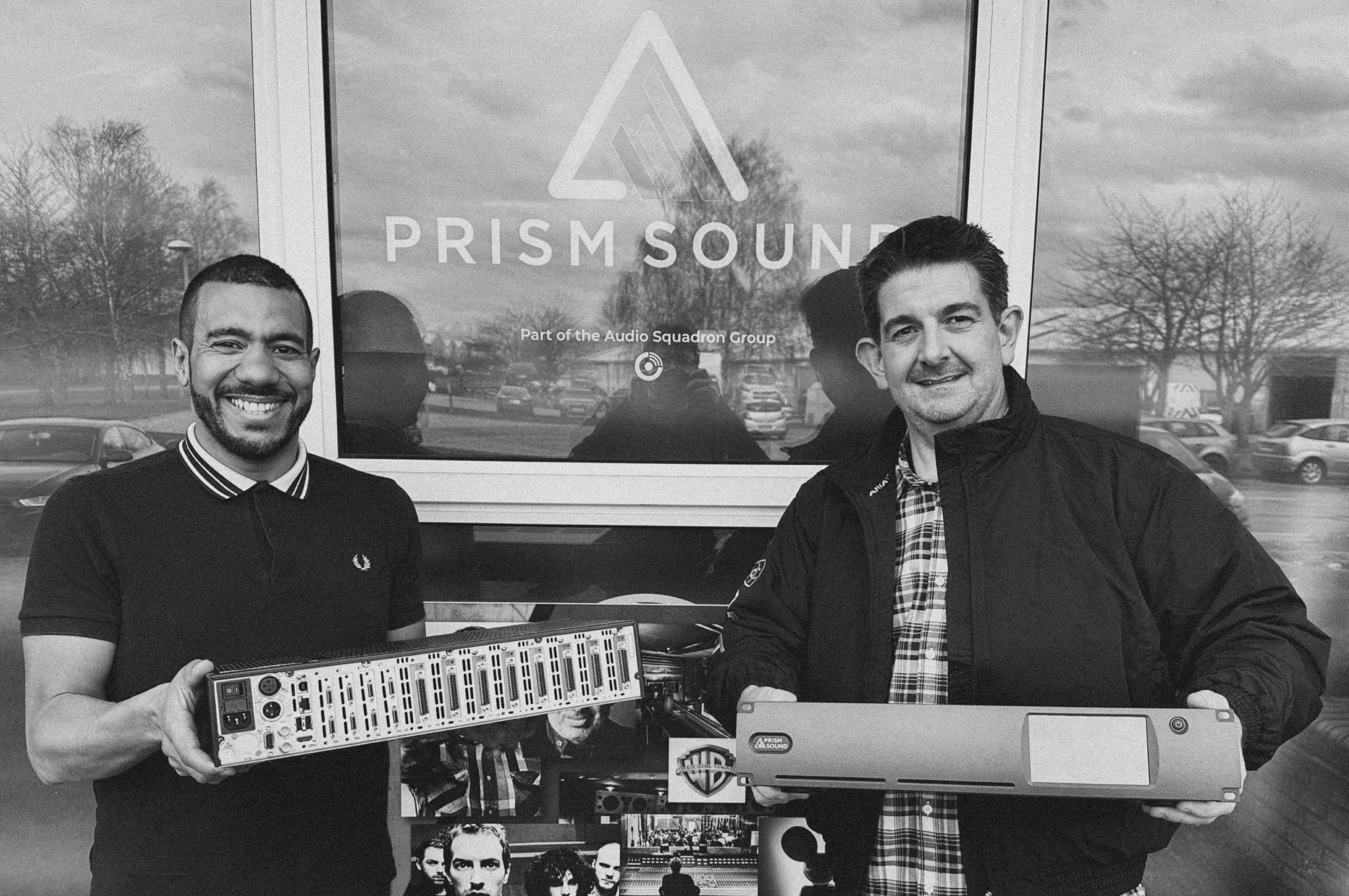
There seems to be a trend with well known “heritage” brands now producing consumer-level gear, I suppose in an effort to offer a gateway into the brand. Would the idea of an “affordable” budget-friendly Prism interface ever be on the cards?
I don’t think anyone at the company could ever categorically state that that’s something we wouldn’t do. However, that is a very crowded and a very congested market and at least for the time being, that is not our focus. That’s not to say we wouldn’t like some professional Prism sound products or a product with a lower entry cost. That that would be great. But that’s a different thing than making a “cheap product”. There is a desire by a lot of big companies to be able to do everything and have a product that can do the conversion and can do the plugins, and be your DSP engine and monitor controller, and can run your workstation… But that comes with compromise. Whilst these people are very smart they probably don’t do any one of those jobs as good as a company that just does one of them. And that’s the challenge with venturing into lower cost end of the market.
Time and time again, we’re asked “do your products sound better” and our response to that is always the same… define “better”. It is entirely feasible that you could buy the most expensive Prism converter and put it alongside the cheapest sound-card money on the market and “prefer” the cheaper option. This is entirely subjective and that of course, is absolutely fine. But, if you asked us “is your product more accurate” then the answer would be a resounding “yes”. And that is because that is all we are interested in and that is our sole focus. We don’t set out ever to make a products that sounds nice, we set out to make a product that has no sound at all. We want to sound like a piece of cable. And so when faced with that question I guess people can sometimes get irritated by our answer!
That’s really the only way you can quantify the term “better”, right? What is measurably more accurate on paper.
Yeah, and we believe that in a professional recording environment, in a mastering studio or archiving facility accuracy is the most important thing, so that’s what we do.
What does the future of Prism look like? Anything else exciting on the horizon?
In terms of what’s in store for this year, adding cards to 128. That is the very next thing we’ll be doing. MADI and mic/line cards are coming soon, with Thunderbolt in the pipeline. We’ve always got an eye on what we’re going to do next. We are at a point with the 128 where we’re already starting to think: “okay, what now?” We still believe that Lyra, Titan, Atlas have a ton of life in them, but they are all built on the Orpheus platform, right? The 128, on the other hand – not only is it new product, but it is a new platform based off which the next generation of Prism Sound products will be built. We can take the AD/DA and clock circuit from the 128 and repackage it into other form factors and other new products, so that’s pretty exciting. That said, Prism Sound do not churn out products at the speed that most of the industry does. We build things to last, but they take a long time to design. What I will say is that our phone lines and inboxes are open: people can talk to us and ask us questions and we listen, and the Dream ADA-128 is testament to this. These things come from conversations with our clients who say they really need something, or “wouldn’t it be cool if…”. In all honesty, our products wouldn’t be half as good if we just locked ourselves away and came out with what we thought was brilliant! We might well completely miss the mark, so it’s vital for us to listen and learn from those who use our products.